Ensuring Safety: Electric Shock Protection and The Role of RCDs
- Hüseyin GÜZEL
- Mar 6, 2024
- 12 min read
Electricity has become an indispensable part of our daily lives, powering our homes, workplaces, and the myriad of devices we use. While electricity provides convenience, it also poses potential risks, with electric shocks being a major concern. In this article, we’ll explore the importance of electric shock protection and the crucial role that Residual Current Devices (RCDs) play in ensuring our safety.

Understanding Electric Shocks: Electric shocks occur when the body becomes part of an electric circuit, typically due to faulty wiring, damaged appliances, or direct contact with live electrical parts. The consequences of electric shocks can range from mild discomfort to severe injury or even fatality.
The content table:
1| Principles of Shock Protection
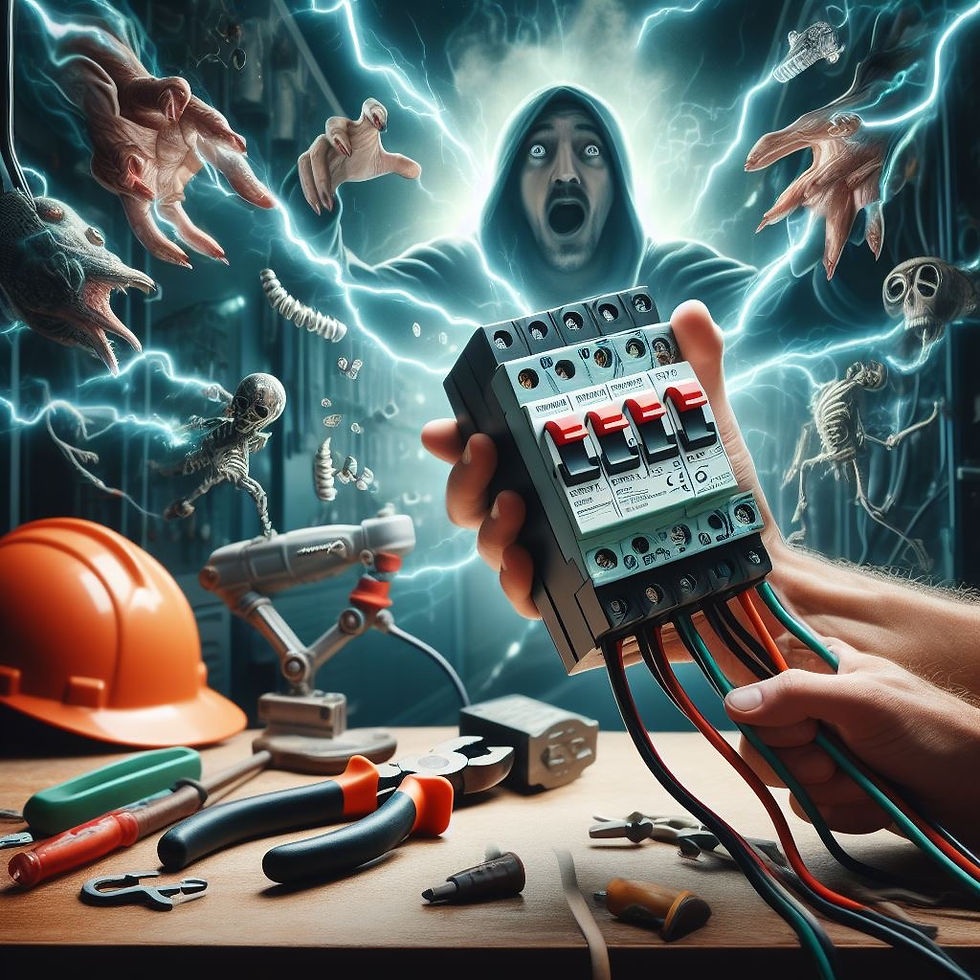
Protection of persons and livestock against electric shock is a fundamental principle in the design of electrical installations in accordance with Bs 7671: Requirements for Electrical Installations, commonly known as The IET Wiring Regulations. use of the correct earthing system is an essential part of this process.
Electric shock may arise from direct contact with live parts, for example when a person touches a live conductor that has become exposed as a result of damage to the insulation of an electric cable.
Alternatively, it may arise from indirect contact if, for example, a fault results in the exposed metalwork of an electrical appliance, or even other metalwork such as a sink or plumbing system becoming live. In either case, there is a risk of an electric current flowing to earth through the body of any person who touches the live conductor or live metalwork. (See Figure 1).
Fuses and circuit breakers provide the first line of defence against indirect contact electric shock. If the installation is correctly earthed (i.e. all the exposed metalwork is connected together and to the main earth terminal of the installation) then an indirect contact fault will cause a very high current to flow to earth through the exposed metalwork. This will be sufficient to ‘blow’ the fuse or trip the circuit breaker, disconnecting that part of the installation within the time specified in BS 7671 and so protecting the user.
Fuses and circuit breakers cannot provide protection against the very small electric currents flowing to earth through the body as a result of direct contact. RCDs, provided they have been selected correctly, can afford this protection as described in the previous chapter. They also provide protection against indirect contact under certain installation conditions where fuses and circuit-breakers cannot achieve the desired effect, for example where the earthing systems described above are ineffective.

2| Earthing Systems

For a full understanding of electric shock protection, it is necessary to consider the different types of earthing systems in use. BS 7671 lists five types as described below:

In this arrangement a single protective earth and neutral (pEN) conductor is used for both the neutral and protective functions, all exposed-conductive-parts being connected to the pEN conductor. It should be noted that in this system an RCD is not permitted since the earth and neutral currents cannot be separated.

With this system the conductors for neutral and protective earth (PE) circuits are separate and all exposed-conductive parts are connected to the PE conductor. This system is the one most commonly used in the UK, although greater use is being made of the TN-C-S arrangement due to the difficulties of obtaining a good substation earth.

The usual form of a TN-C-S system is where the supply is TN-C and the
arrangement of the conductors in the installation is TN-S. This system is often described as a protective multiple earthing (pME) system. This is incorrect since pME is a method of earthing.

In a TT system, the electricity supply provider and the consumer must both provide earth electrodes at appropriate locations, the two being electrically separate. All exposed-conductive parts of the installation are connected to the consumer’s earth electrode.

Unlike the previous systems, the IT system is not permitted, except under special license, for the low voltage supply in the UK. It does not rely on earthing for safety, until after the occurrence of a first fault, as the supply side is either completely isolated from earth or is earthed through a high impedance.
3| Protection Against Direct and Indirect Contact

It is a fundamental requirement of BS 7671 that all persons and livestock are protected against electric shock in any electrical installation. This is subject to the installation being used with reasonable care and having regard to the purpose for which it was intended. When considering protection against electric shock, it is necessary to understand the difference between ‘direct contact’ and ‘indirect contact’, which was first introduced by the 15th Edition of the IEE Wiring Regulations in 1981 (See Figure 1).
Direct contact electric shock is the result of simultaneous contact by persons or livestock with a normally live part and earth potential. As a result, the victim will experience nearly full mains voltage across those parts of the body which are between the points of contact.
Indirect contact electric shock results from contact with an exposed conductive part made live by a fault condition and simultaneous contact with earth potential. This is usually at a lower voltage.
Protection against direct contact electric shock (now defined as Basic Protection in BS 7671) is based on normal common sense measures such as insulation of live parts, use of barriers or enclosures, protection from obstacles or protection by placing live parts out of reach. As a result, under normal conditions, it is not possible to touch the live parts of the installation or equipment inadvertently.
Protection against indirect contact electric shock (now defined as Fault Protection in BS 7671) is slightly more complicated hence a number of options are given in BS 7671 for the installation designer to consider.
The majority of these require specialist knowledge or supervision to be applied effectively. The most practical method for general use is a combination of protective earthing, protective equipotential bonding and automatic disconnection of supply. This method which provides very effective protection when properly applied, requires consideration of three separate measures by the circuit designer:
Protective Earthing
Protective equipotential bonding
Automatic disconnection in the event of a fault
Protective Earthing requires all exposed-conductive parts (generally metallic) of the installation to be connected to the installation main earth terminal by means of circuit protective conductors (cpcs).
The main earth terminal has to be effectively connected to Earth. Typical examples of exposed conductive parts include:
Conduits and trunking
Equipment enclosures
Class I luminaires
The casings and framework of current equipment
Protective equipotential bonding minimises the risk of electric shock by connecting extraneous-conductive- parts (generally metalwork that is in contact with the Earth) within the location, to the main earth terminal of the installation. This means that under fault conditions the voltage that is present on the metal casings of electrical equipment is substantially the same as that present on all extraneous-conductive parts.
Theoretically, a person or animal coming into simultaneous contact with the faulty equipment and other earthed metalwork will not experience an electric shock because of the equipotential cage formed by the bonding. In practice, however, a small ‘touch’ voltage will be present due to differing circuit impedances.
Automatic disconnection of supply is most important for effective shock protection against indirect contact. It involves ensuring that the faulty circuit is disconnected within a specified safe time following a fault to earth. What constitutes a safe time depends on many factors and those who require detailed information on this should consult the definitive documents, IEC TS 60479 series and BS 7671 Regulation 411.3.2.
When using an overcurrent protective device e.g. a fuse or circuit breaker, for automatic disconnection, in order to meet the requirements of BS 7671, it is necessary to ensure that these devices can operate within a specified time in the event of an earth fault. This is achieved by making sure that the earth fault loop impedance is low enough to allow sufficient fault current to flow. It is possible to calculate the appropriate values using the published time/current curves of the relevant device. Alternatively, BS 7671 publishes maximum values of earth fault loop impedance (Z s) for different types and ratings of overcurrent devices. Reference should be made to the time/current curves published in BS 7671 or by the manufacturers of protective devices.
4| The Role of RCDs
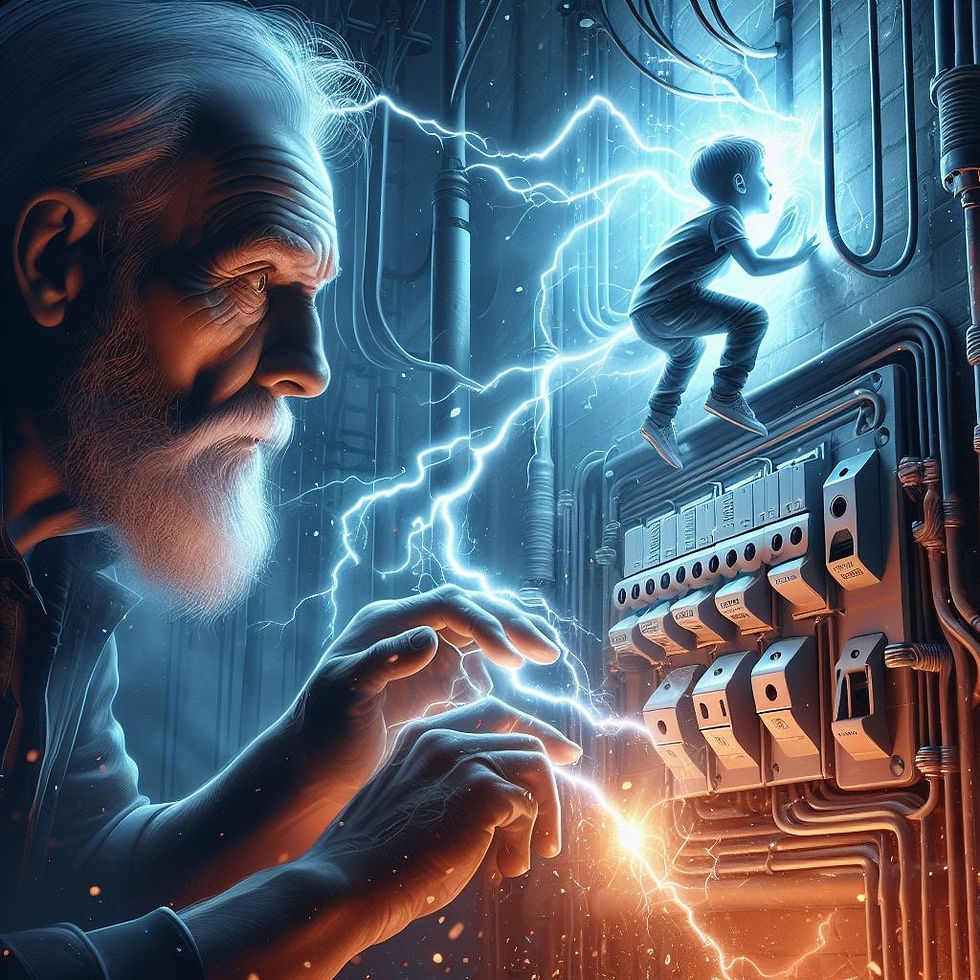
Residual Current Devices, commonly known as RCDs or GFCIs (Ground Fault Circuit Interrupters), act as a crucial line of defense against electric shocks. These devices continuously monitor the flow of electric current and instantly disconnect the power supply if they detect an imbalance, signaling a leakage of current, which could potentially lead to a dangerous situation.
Key Features of RCDs:
Quick Response: RCDs are designed to respond swiftly, disconnecting the power within milliseconds of detecting a fault. This rapid response significantly reduces the risk of electric shock.
Comprehensive Protection: RCDs provide protection not only for individuals but also for electrical appliances and wiring systems. By preventing prolonged exposure to faulty circuits, they contribute to overall electrical safety.
Versatility: RCDs can be installed in various locations, including homes, offices, and industrial settings. They are available in different types, catering to specific needs such as portable RCDs for temporary setups.
Tips for Using RCDs Effectively:
Regular Testing: It’s crucial to regularly test RCDs to ensure they function correctly. Most devices come with a test button that should be pressed at least once a month.
Professional Installation: RCDs should be installed by qualified electricians to guarantee proper functioning and adherence to safety standards.
Sensitivity: Different RCDs have varying sensitivity levels. Choosing the right device for specific applications is essential to ensure effective protection without unnecessary tripping.
Electric shock protection is a shared responsibility, and incorporating Residual Current Devices is a proactive step towards creating safer environments. Whether in residential, commercial, or industrial settings, the implementation of RCDs significantly reduces the risk of electric shocks, safeguarding lives and property. Prioritizing electrical safety through awareness, regular maintenance, and the use of advanced protective devices ensures that the power we rely on remains a source of convenience without compromising on safety.
4.1| The Residual Current Devices (RCDs) Role and Indirect Contact Shock Protection
Indirect contact protection by fuses or circuit-breakers is dependent on circuit earth fault loop impedances being within the parameters laid down by BS 7671. Where these values cannot be achieved or where there is some doubt about their stability, then an alternative method is required. It is in this situation that the RCD offers the most practical solution because it has the ability to operate on circuits having much higher values of earth fault loop impedance.
The basis of RCD protection in this situation is to ensure that any voltage, exceeding 50 V that arises due to earth fault currents, is immediately disconnected. This is achieved by choosing an appropriate residual current rating and calculating the maximum earth loop impedance that would allow a fault voltage of 50 V. This is calculated by using a simple formula given in BS 7671 Regulation 411.5.3.
Ra × IΔn ≤ 50V
Where,
Ra is the sum of the resistances of the earth electrode and the protective conductor connecting it to the exposed conductive part (in ohms)
IΔn is the rated residual operating current of the RCD (amps)
Note: Where Ra is not known it may be replaced by Zs.
Maximum values of Zs for the basic standard ratings of RCDs are given in Table 1, unless the manufacturer declares alternative values.

Note 1: Figures for Zs result from the application of Regulation 411.5.3(i) and 411.5.3(ii).
Note 2: *The resistance of the installation earth electrode should be as low as practicable. A value exceeding 200 ohms may not be stable. Refer to Regulation 542.2.4.
The use of a suitably rated RCD for indirect contact shock protection will permit much higher values of Z s than could be expected by using overcurrent protective devices. In practice, however, values above 200 ohms will require further consideration. This is particularly important in installations relying on local earth electrodes (TT systems) where the relatively high values of Z s make the use of an RCD absolutely essential.
4.2| The Residual Current Devices (RCDs) Role and Direct Contact Shock Protection
The use of RCDs with a rated residual operating current of 30 mA or less is recognised as additional protection against direct contact shock. Regulation 415.1.1 refers.
Direct contact shock is the result of persons or livestock inadvertently making contact with normally live parts with one part of the body and, at the same time, making contact with earth potential with another part of the body. Under these circumstances, the resulting electric shock will be at full mains potential and the actual current flowing to earth will be of the order 230 mA because of the relatively high body impedance involved. It has already been shown in Section 2.3 that currents as low as 40/50 mA can result in electrocution under certain circumstances. A 30 mA RCD will disconnect an earth fault current before the levels at which fibrillation occurs are reached.
The nominal rating of 30 mA has thus become the internationally accepted norm for RCDs intended to provide additional protection against the risk of electrocution.
However, the rated operating current is not the only consideration; the speed of tripping is also very important. If ventricular fibrillation is to be avoided.
Examples of types of fault condition where the RCD can be of particular benefit are listed in other chapters.
One example is situations where basic insulation has failed either through deterioration or, more commonly, through damage. An example of this is when a nail is driven through a partition wall and penetrates a cable. This will cause a first-fault condition due to failure of the basic insulation. The result of this is that there is now a strong possibility that the nail will become live by contacting the live conductor. Any subsequent contact by a person presents a risk of electrocution or injury by direct contact. An RCD will provide additional protection and significantly reduce the risk of injury or death because it will trip when a dangerous level of current flows to earth through the person in contact with the nail.
This type of RCD protection is identical to the more common situation where a flexible cable is damaged (for example by a lawn mower) and exposes live conductors. Here again the RCD provides protection of anybody who comes into contact with the exposed live conductors.
The extra protection provided by RCDs is now fully appreciated and this is recognised in BS 7671 Regulation 415.1.
It must be stressed, however, that the RCD should be used as additional protection only and not considered as a substitute for the basic means of direct contact shock protection (insulation, enclosure etc).
4.3| RCDs in Reduced and Extra-Low Voltage Applications
In normal use, dangerous touch voltages should not occur on electrical equipment intended for use with, and supplied from, an extra-low (not exceeding 50 V AC) or reduced voltage (not exceeding 63.5 V to earth in three-phase systems or 55 V to earth in single-phase systems) source. Such circuits are known as:
Separated extra-low voltage (SELV), in which the circuit is electrically separated from earth and from other systems.
Protective extra-low voltage (PELV), as SELV except that the circuit is not electrically separated from earth.
Functional extra-low voltage (FELV), an extra-low voltage system in which not all of the protective measures of SELV or PELV have been applied.
Reduced low-voltage system a voltage system in which all exposed-conductive parts are connected to the earth and protection against indirect contact shock is provided by automatic disconnection by an overcurrent protective device or RCD.
SELV, PELV and reduced low voltage system arrangements involve electrical separation of the final circuit normally by means of a safety-isolating transformer. In normal use, the transformer prevents the appearance of any dangerous touch voltages on either the electrical equipment or in the circuit. Although extremely rare, a fault occurring within the safety isolating transformer may result in a dangerous touch voltage, up to the supply voltage, appearing within the circuit or on the electrical equipment. Where additional protection against this risk is required, or in the case of a reduced low voltage system, an RCD with a rated residual current of 30 mA or less, can be installed in the primary circuit to achieve a 5 s disconnection time.
In PELV, FELV and reduced low voltage systems an RCD can, if required, be connected into the secondary circuit of the transformer. This will provide additional protection against electric shock under all conditions:
Shock protection if there is a failure of the transformer and mains voltage-appears on the secondary side.
Protection against indirect contact from the low-voltage secondary voltage.
Additional protection against direct contact from the low-voltage secondary voltage.
It must be remembered that, since a FELV circuit is not isolated from the mains supply or earth, it presents the greatest risk from electric shock of all of the ELV methods.
An RCD can also provide this additional protection in a SELV circuit and its electrical equipment but in this case a double-fault condition, which need not normally be considered, would have to occur before the RCD could operate.
Manufacturer’s guidance should always be sought when applying RCDs in extra-low and reduced voltage applications, to confirm that devices will operate at these voltages. This is particularly important with respect to the test button since its correct operation depends on the supply voltage.
4.4| RCDs in Electric Vehicle Charging
Particular care must be taken in the selection of the type of RCD to be used in electric vehicle charging installations. BS7671 does not permit the use of RCD. Type AC for this application. Where RCDs are used, BS7671 requires:
RCD Type B; or
RCD Type A and appropriate equipment that provides disconnection of the supply in case of DC fault current above 6 mA
Comments