Required Steps to Ensure Effective Transformer Grounding
- Hüseyin GÜZEL
- Jan 2, 2022
- 12 min read
An electrical substation is a critical resource in a power system. Safe operation of a substation calls for a properly designed and installed grounding system. A well-designed grounding system will ensure the reliable performance of the substation over its entire service life.

How does good grounding improve substation reliability?
A good grounding path of sufficiently low impedance ensures fast clearing of faults. A fault remaining in the system for a long may cause several problems including those of power system stability. Faster clearing thus improves overall reliability.
It also ensures safety.
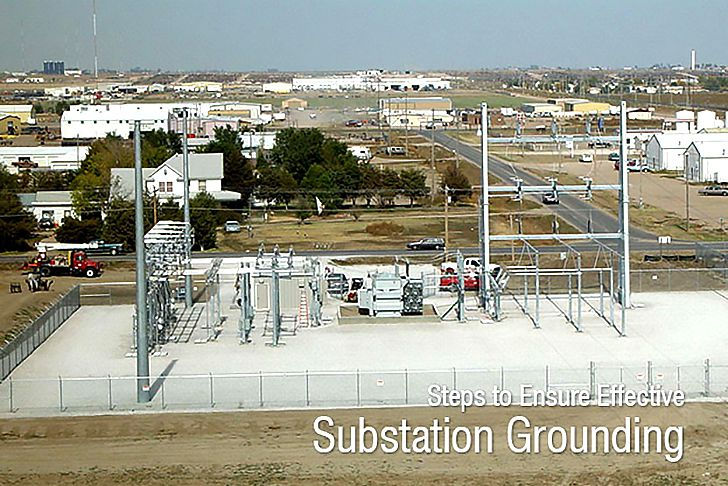
A ground fault in equipment causes the metallic enclosure potential to rise above the ‘true’ ground potential. An improper grounding results in a higher potential and also results in delayed clearing of the fault (due to insufficient current flow).
This combination is essentially unsafe because any person coming into contact with the enclosure is exposed to higher potentials for a longer duration.
Therefore, substation reliability and safety must be as ‘built-in’ as possible by good grounding scheme, which in turn will ensure faster fault clearing and low enclosure potential rise

Ensuring Proper Grounding
The following steps, when put into practice, will ensure a reliable, safe and trouble-free substation grounding system:
Size conductors for anticipated faults
Use the right connections
Ground rod selection
Soil preparation
Attention to step and touch potentials
Grounding using building foundations
Grounding the substation fence
Special attention to operating points
Surge arrestors must be grounded properly
Grounding of cable trays
Temporary grounding of normally energized parts
1| Size Conductors For Anticipated Faults
Conductors must be large enough to handle any anticipated faults without fusing (melting).
Failure to use proper fault time in design calculations creates a high risk of melted conductors. Two aspects govern the choice of conductor size: the first is the fault current that will flow through the conductor and the second is the time for which it can flow.

The fault current depends on the impedance of the ground fault loop. The time of current flow is decided by the setting of the protective relays/circuit-breaking devices, which will operate to clear the fault.
The IEEE 80 suggests using a time of 3.0 s for the design of small substations. This time is also equal to the short-time rating of most switchgear.
2| Use the Right Connections
It is very evident that the connections between conductors and the main grid and between the grid and ground rods are as important as the conductors themselves in maintaining a permanent low-resistance path to the ground.
The basic issues here are:
The type of bond used for the connection of the conductor in its run, with the ground grid and with the ground rod
The temperature limits, which a joint can withstand.
The most frequently used grounding connections are mechanical pressure type(which will include bolted, compression and wedge-type construction) and exothermically welded type.
Pressure-type connections produce a mechanical bond between conductor and connector by means of a tightened bolt nut or by crimping using hydraulic or mechanical pressure. This connection either holds the conductors in place or squeezes them together, providing surface-to-surface contact with the exposed conductor strands.
On the other hand, the exothermic process fuses the conductor ends together to form a molecular bond between all strands of the conductor.
Temperature limits are stated in standards such as IEEE 80 and IEEE 837 for different types of joints based on the joint resistance normally obtainable with each type. Exceeding these temperatures during the flow of fault currents may result in damage to the joint and cause the joint resistance to increase, which will result in further overheating.
The joint will ultimately fail and result in grounding system degradation or total loss of ground reference with disastrous results.

3| Ground Rod Selection
In MV and HV substations, where the source and load are connected through long overhead lines, it often happens that the ground fault current has no metallic path and has to flow through the groundmass (earth). This means that the ground rods of both source and load side substations have to carry this current to or from the groundmass
The ground rod system should be adequate to carry this current and ground resistance of the grounding system assumes importance
The length, number and placement of ground rods affect the resistance of the path to earth. Doubling of ground rod length reduces resistance by a value of 45%, under uniform soil conditions. Usually, soil conditions are not uniform and it is vital to obtain accurate data by measuring ground rod resistance with appropriate instruments.
For maximum efficiency, grounding rods should be placed no closer together than the length of the rod. Normally, this is 10 ft (3 m). Each rod forms an electromagnetic shell around it, and when the rods are too close, the ground currents of the shells interfere with each other.
It should be noted that as the number of rods is increased, the reduction of ground resistance is not in inverse proportion. Twenty rods do not result in 1/20th of the resistance of a single rod but only reduce it by a factor of 1/10th.
For economic reasons, there is a limit to the maximum distance between rods.
Normally, this limit is taken as 6 m. At more than 6 m, the cost of the additional conductor needed to connect the rods makes the design economically attractive.
In certain cases, the substation layout may not have the required space and acquiring the needed space may involve substantial expense. Four interconnected rods on 30 m centres will reduce resistivity 94% over one rod but require at least 120 m of the conductor.
On the other hand, four rods placed 6 m apart will reduce resistivity 81% over one rod and use only 24 m of the conductor.
4| Soil Preparation
Soil resistivity is an important consideration in substation grounding system design. The lower the resistivity, the easier it is to get a good ground resistance.
Areas of high soil resistivity and those with ground frost (which in turn causes the soil resistivity to increase by orders of magnitude) need special consideration. The highest ground resistivity during the annual weather cycle should form the basis of the design since the same soil will have much higher resistivity during dry weather when the percentage of moisture in the ground becomes very low
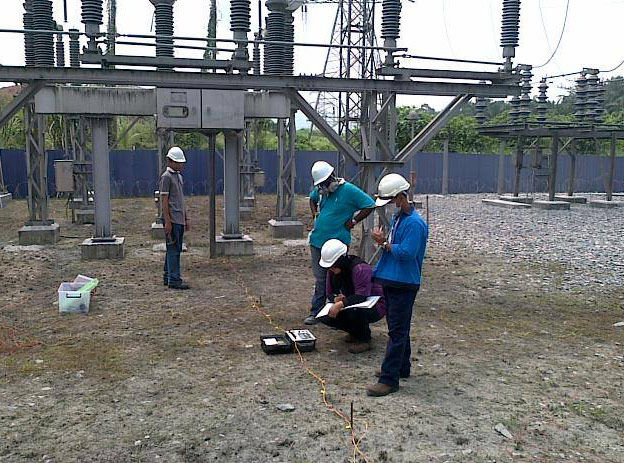
Grounding Tests – Earth Potential and Grounding Mesh Effectiveness (courtesy of DCS Engineering Sdn Bhd – www.dcsesb.com)
One approach to take care of this problem is to use deep driven ground rods so that they are in contact with the soil zone deep enough to remain unaffected by surface climate.
The other approach is to treat the soil around the ground rod with chemical substances that have the capacity to absorb atmospheric/soil moisture. The use of chemical rods is one such solution
5| Attention to Step and Touch Potentials
Limiting step and touch potential to safe values in a substation is vital to personnel safety.
Step potential is the voltage difference between a person’s feet and is caused by the voltage gradient in the soil at the point where a fault enters the earth. The potential gradient is steepest near the fault location and thereafter reduces gradually. Just 75 cm away from the entry point, voltage usually will have been reduced by 50%.
Thus at a point of 75 cm from the fault (which is less than the distance of a normal step), a fatal potential of a few kilovolts can exist.
Touch potential represents the same basic hazard, except the potential exists between the person’s hand and his or her feet. This happens when a person standing on the ground touches a structure of the substation, which is conducting the fault current into the ground (for example, when an insulator is fixed on a gantry flashover, the gantry dissipates the current to earth).
Since the likely current path within the human body runs through the arm and heart region instead of through the lower extremities, the danger of injury or death is far greater in this case. For this reason, the safe limit of touch potential is usually much lower than that of step potential.
In both situations, the potential can essentially be greatly reduced by an equipotential wire mesh safety mat installed just below ground level.
This mesh will have to be installed in the immediate vicinity of any switches or equipment a worker might touch, and connect to the main ground grid. Such an equipotential mesh will equalize the voltage along the worker’s path and between the equipment and his or her feet. With the voltage difference (potential) thus essentially eliminated, the safety of personnel is virtually guaranteed.
An equipotential wire mesh safety mat is usually fabricated from #6 or #8 AWG copper or copper-clad wire to form a 0.5 ×0.5 m or 0.5 ×1 m mesh. Many other mesh sizes are available.
To ensure continuity across the mesh, all wire crossings are brazed with a 35% silver alloy. Interconnections between sections of mesh and between the mesh and the main grounding grid should be made so as to provide a permanent low-resistance high-integrity connection
6| Grounding Using Building Foundations
Concrete foundations below ground level provide an excellent means of obtaining a low-resistance ground electrode system. Since concrete has a resistivity of about 30 Ωm at 20 °C, a rod embedded within a concrete encasement gives a very low electrode resistance compared to most rods buried in the ground directly.
Since buildings are usually constructed using steel-reinforced concrete, it is possible to use the reinforcement rod as the conductor of the electrode by ensuring that an electrical connection can be established with the main rebar of each foundation.
The size of the rebar as well as the bonding between the bars of different concrete members must be done so as to ensure that ground fault currents can be handled without excessive heating.
Such heating may cause weakening and eventual failure of the concrete member itself. Alternatively, copper rods embedded within concrete can also be used.
The use of ‘Ufer’ grounds (named after the person who was instrumental in the development of this type of grounding practice) has significantly increased in recent years. Ufer grounds utilize the concrete foundation of a structure plus building steel as a grounding electrode.
Even if the anchor bolts are not directly connected to the reinforcing bars (rebar), their close proximity and the conductive nature of concrete will provide an electrical path.
There are a couple of issues to be considered while planning for grounding using the foundations as electrodes. A high fault current (lightning surge or heavy ground fault) can cause moisture in the concrete to evaporate suddenly to steam
This steam, whose volume is about 1800 times of its original volume when existing as liquid, produces forces that may crack or otherwise damage the concrete. The other factor has to do with ground leakage currents. The presence of even a small amount of DC current will cause corrosion of the rebar. Because corroded steel swells to about twice its original volume, it can cause extremely large forces within the concrete.
Although AC leakage will not cause corrosion, the earth will rectify a small percentage of the AC to DC. In situations where the anchor bolts are not bonded to the rebar, concrete can disintegrate in the current path.
Damage to concrete can be minimized either by limiting the duration of fault current flow (by suitable sensitive and fast-acting protective devices) or by providing a metallic path from the rebar through the concrete to an external electrode.
That external electrode must be sized and connected to protect the concrete’s integrity. Proper design of Ufer grounds provides for connections between all steel members in the foundation and one or more metallic paths to an external ground rod or main ground grid.
Excellent joining products are available in the market, which is specially designed for joining rebars throughout the construction. By the proper joining of the rebars, exceptionally good performance can be achieved.
An extremely low resistance path to earth for lightning and earth fault currents is ensured as the mass of the building keeps the foundation in good contact with the soil.
7| Grounding the Substation Fence

Metallic fences of substations should be considered just as other substation structures. The reason for this is that the overhead HV lines entering or leaving a substation may snap and fall on the fence. Unless the fence is integrated with the rest of the substation grounding system, a dangerous situation may develop. Persons or livestock in contact with the fence may receive dangerous electric shocks.
Utilities vary in their fence-grounding specifications, with most specifying that each gate post and corner post, plus every second or third line post, be grounded. All gates should be bonded to the gate posts using flexible jumpers. All gate posts should be interconnected. In the gate swing area, an equipotential wire mesh safety mat can further reduce hazards from step and touch potentials when opening or closing the gate.
It is recommended that the fence ground should be tied into the main ground grid, as it will reduce both grid resistance and grid voltage rise. Internal and perimeter gradients must be kept within safe limits because the fence is also at full potential rise.
This can be accomplished by extending the mesh with a buried perimeter conductor that is about 1 m outside the fence and bonding the fence and the conductor together at close intervals (so that a person or grazing animal touching the fence will stand on the equipotential surface so created)
8| Special Attention to Operating Points
To protect the operator in case of a fault, it should be ensured that he is not subjected to high touch or step potentials when a fault happens in the equipment he is operating. This calls for use of a safety mesh close to these operating points on which the operator will stand and operate the equipment.
There are four types of safety mats.
A steel grate or plate on supporting insulators. This works only if the operator can be kept completely isolated on the grate. Therefore, insulators must be kept clean. Any vegetation in the vicinity should be cut or eliminated completely (this approach is similar to the insulating rubber mats placed in front of most indoor electrical equipment). Safety is ensured by increasing the resistance of the current path so that the current flowing through the operator’s body into the ground does not exceed safe values.
A steel grate on the surface, permanently attached to the grounded structure. This arrangement has the operator standing directly on the grate.
Bare conductor buried (in a coil or zig-zag pattern) under the handle area and bonded to the grounded structure.
Prefabricated equipotential wire mesh safety mat buried under the handle area and bonded to the grounded structure. This is likely to be the least expensive choice.
In all but the first arrangement, both the switch operating handle and the personnel safety grate (or mat) should be exothermically welded to structural steel, thus ensuring nearly zero voltage drop.
9| Surge Arrestors Must be Grounded Properly!
When there are a surge in the electrical system (by indirect lightning strikes or due to switching) surge arrestors placed near all critical equipment divert surge energy to the ground and protect the equipment from being subjected to the surges.
Usually, surges involve a very fast rise time during which the current changes from zero to extremely high values of several kiloamperes. It is, therefore, necessary that the conducting path from the grounding terminal of the surge arrestor to the earth must have minimum impedance.
Even a small amount of self-inductance offered by a grounding conductor will mean very high impedance because of the steep wavefront of the surge and very high voltages from appearing in the grounding system (albeit briefly). To dissipate the surge current with minimum voltage drop, each surge arrestor ground lead should have a short direct path to earth and should be free of sharp bends (bends act like a coil and increase the inductance).
Often surge arrestors are mounted directly on the tank of transformers, close to the HV terminal bushings. In these cases, the transformer tanks and related structures act as the grounding path.
It must be ensured that multiple and secure paths to the ground are available (this includes making effective connections).
Whenever there is any question about the adequacy of these paths, it is recommended to use a separate copper conductor between the arrestor and the ground terminal (or main grounding grid). Since steel structures (due to their multiple members) have lower impedance than a single copper conductor, the grounding conductors should preferably be interconnected to the structure near the arrestor.
10| Grounding of Cable Trays
The NEC vide Art. 318 specifies the requirements for cable trays and their use in reducing the induced voltages during a ground fault. All metallic tray sections must be bonded together with proper conducting interconnections. The mechanical splice plates by themselves may not provide an adequate and reliable ground path for fault currents.
Therefore, the bonding jumpers (either the welded type used on steel trays or the lug type) must be placed across each spliced tray joint. If a metallic tray comes with a continuous grounding conductor, the conductor can be bonded inside or outside the tray. When cable tray covers are used, they should be bonded to the tray with a flexible conductor. The trays should also be bonded to the building steel (usually at every other column)
11| Temporary Grounding of Normally Energized Parts
When personnel work on high-voltage electric structures or equipment, any conductive bodies should be grounded as a measure of safety.

This is done so that in the event of the circuit becoming life due to inadvertent switching, the safety of personnel (in contact with the parts, which would become life) is ensured.
The usual grounding method is to attach a flexible insulated copper cable with a ground clamp or lug on each end. These flexible jumpers require periodic inspection and maintenance. For cable connections to clamps, welded terminations (either a welded plain stud or a threaded silicon bronze stud welded to the conductor end) will provide a secure, permanent connection.
The clamp or lug is solidly connected to the ground, then the other clamp is attached to the cable being grounded.
Source: Practical Grounding, Bonding, Shielding and Surge Protection – G. Vijayaraghavan; Mark Brown (Get this book at Amazon)
Destek olmak için bana bir kahve ısmarlayabilirsiniz :) ve E-Posta Bültenimize de üye olabilirsiniz...
댓글