The Most Common Power Supply in LV Networks: MV/LV Transformers
- Hüseyin GÜZEL
- Jul 14, 2024
- 8 min read
MV/LV Transformers play a vital role in ensuring that the electricity we use in our homes, businesses, and industries is safe and reliable. By stepping down the medium voltage to a lower, more manageable level, they make it possible for us to power everything from household appliances to industrial machinery. It's fascinating how such technology is integral to our daily lives, isn't it?
In low voltage (LV) networks, the most common power supply is provided by medium voltage to low voltage (MV/LV) transformers. These transformers are essential for converting higher voltage levels from the distribution network to lower voltage levels suitable for end consumers. MV/LV transformers come in various types, including oil-immersed, air-insulated, and resin-insulated dry-type transformers. They play a crucial role in ensuring reliable and efficient power distribution to homes and businesses.
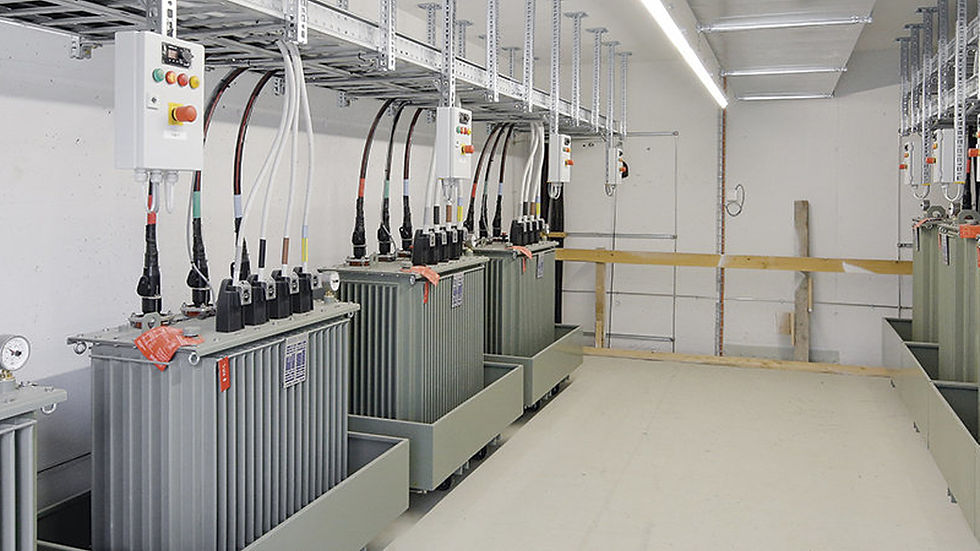
MV/LV transformers are generally divided into three main types based on their construction: oil-immersed transformers, air-insulated transformers, and resin-insulated dry-type transformers.
Oil-immersed transformers: These use a liquid dielectric for insulation and cooling. They are widely used but require protective measures against fire and pollution.
Air-insulated transformers: These use air as the insulating medium and are typically used in environments where fire safety is a concern.
Resin-insulated dry-type transformers: These are solidly insulated with resin, making them suitable for indoor applications where oil or air insulation might not be ideal.
Each type has its specific applications and advantages, ensuring that there is a suitable transformer for various needs in low-voltage networks.
The general term "power supply" in LV networks refers to the supply of electrical energy. The power supply, and more generally the different supplies, are provided by sources such as mains supply, batteries, generator sets, etc., which can include MV/LV transformers, diesel generator sets, and UPSs.
This technical article will explain the most common power supply for LV networks provided by an MV/LV transformer. Don't be confused; the same transformer, with or without some modifications, can also be used as a backup power supply, a special power supply for safety services, or an auxiliary power supply.
Let’s see the most common power supply source – transformers that are used in MV/LV networks.
We won't delve into the basics of a transformer. Just one sentence: A transformer is an electromagnetic induction device that transfers electrical power between two different voltage systems at the same frequency.
MV/LV transformers are generally divided into three types depending on their construction: Oil, Air-insulated and resin-insulated dry-type transformers.
Table of Contents:
1. Oil Transformers
The magnetic circuit and windings are immersed in a liquid dielectric, which provides insulation and dissipates the heat losses of the transformer.
The liquid you're referring to expands with changes in load and ambient temperature. Due to the prohibition of PCBs and TCBs, mineral oil is commonly used. However, it is flammable and necessitates protective measures to mitigate the risks of fire, explosion, and pollution.
The most commonly used protective measures are the DGPT or DGPT2 sensors, which monitor gas, pressure, and temperature with one or two sensing levels for temperature. This system cuts off the low voltage (LV) load at the first level and the medium voltage (MV) supply at the second level when a fault occurs inside the transformer. A holding tank is used to recover all the liquid dielectric.
Of the four types of immersed transformers:
Free-breathing transformers,
Gas cushion transformers,
Transformers with expansion tanks and
Transformers with integral filling, only the latter are currently installed.

Structural Standards for Immersed Transformers
Power from 50 to 2500 kVA (25 kVA possible):
Primary voltage up to 36 kV
Secondary voltage up to 1.1 kV
Power > 2500 kVA:
HV voltage greater than 36 kV
IEC 60076-1, IEC 60076-2, IEC 60076-3, IEC 60076-4, IEC 60076-5
1.1 Free Breathing Transformers
When air enters the surface of the oil, the cover allows the liquid to expand without overflowing. This process, known as "breathing" causes the humidity in the air to mix with the oil, leading to a deterioration in the dielectric strength of the transformer oil. This is because moisture in the oil reduces its electrical insulating properties, which can compromise the transformer's performance and longevity.
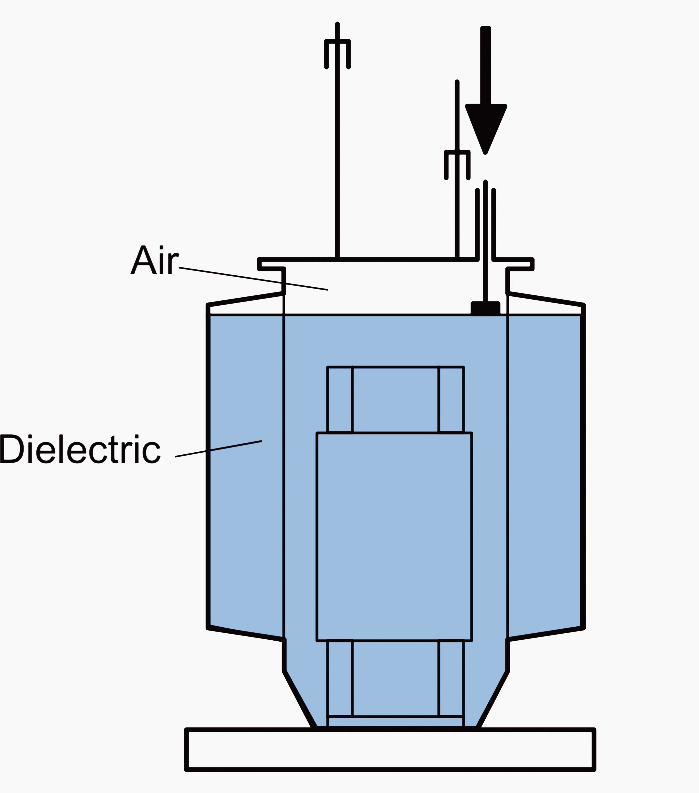
1.2 Gas Cushion Transformers
The tank is sealed, and a cushion of neutral gas compensates for the variation in the volume of the dielectric, reducing the risk of leaks.

1.3 Transformers with Expansion Tank
To mitigate the previous disadvantages, an expansion tank reduces air/oil contact and absorbs overpressure. However, the dielectric fluid continues to oxidize and absorb water. Adding a desiccant breather helps limit this issue but requires regular maintenance.

1.4 Transformers with Integral Filling
Since the tank is completely filled with liquid dielectric and hermetically sealed, there is no risk of oil oxidation. This setup effectively prevents any exposure to air, ensuring the oil remains stable and uncontaminated.
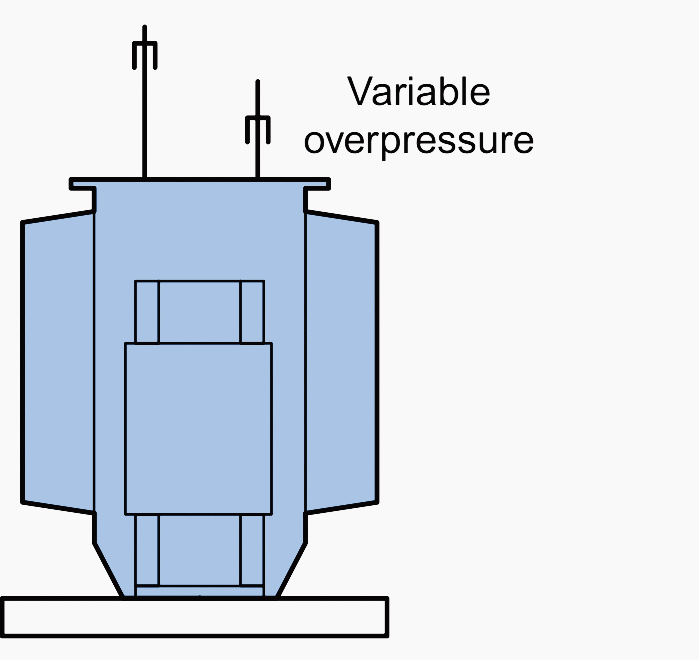
The overpressure caused by the expansion of the liquid is absorbed by the folds of the tank.

2. Air Insulated Transformers
The windings of air transformers are insulated through the wrapping of the windings themselves, the installation of plastic partitions, and adherence to proper insulation distances.
These types are of limited use because their specific construction characteristics make them very sensitive to humidity, even limited pollution, and chemically aggressive substances. In fact, the absorption of humidity and the deposition of dust can lower the dielectric coefficient of the insulating materials used.
A careful commissioning procedure must be followed to avoid affecting the operation, such as drying the windings using heating elements installed on the transformer.

3. Cast Resin Transformers
Dry-type transformers, often referred to as cast resin transformers, have one or more enclosed windings. Thanks to advancements in construction techniques, these transformers are increasingly popular due to their reliability, lower environmental impact compared to oil transformers, and reduced risks of fire and environmental pollution.
Medium-voltage windings, made with wire coils or, preferably, insulated aluminum strips, are placed in a mold into which epoxy resin is poured under vacuum to prevent gas inclusions in the insulation. The windings are then enclosed in a cylindrical, sealed, and mechanically strong enclosure with a smooth surface that prevents dust accumulation and resists the action of pollutants.
Low-voltage windings are typically made from a single aluminum sheet that matches the height of the coil. This sheet is insulated with appropriate materials and undergoes heat treatment to ensure proper insulation and performance.
That's correct! Cast resin transformers are designed with class F insulation, which can withstand temperatures up to 155°C. This allows for a maximum temperature rise of 100°K, ensuring efficient and safe operation. Is there anything specific you'd like to know about these transformers?
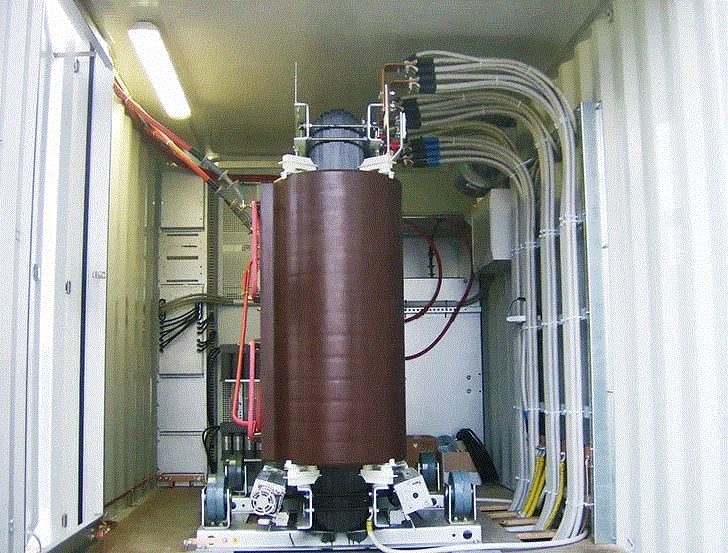
3.1 Applications
Cast resin transformers are highly versatile and reliable, making them suitable for a wide range of applications. They are commonly used in power distribution systems, power generation, rectification processes, and traction systems. Additionally, they are ideal for special requirements in various industries due to their robust performance and safety features.
Distribution of Electrical Power
Service sector: hospitals, banks, schools, shopping and cultural centres
Infrastructures: airports, military installations, ports and off-shore installations
Industry in general
Conversion and Rectification
Air conditioning systems
Continuity units
Railways, underground railways, tramways and cable cars
Lifting and pumping systems
Welding lines
Induction furnaces
Naval propulsion
Step-up Transformers for Power Production
Wind parks
Photovoltaic systems
Cogeneration systems
Industrial applications
4. Medium-Voltage Winding
Using strips instead of wire for medium-voltage (MV) windings reduces the stress on the insulation between the turns. This is because strips provide a more uniform distribution of electrical stress, which helps in maintaining the integrity of the insulation.
In traditional windings, made with a circular-section conductor, each layer of the winding is made up of a number n of turns side by side.
In windings made with strip conductors, each layer consists of a single turn. If the voltage of a single turn of a winding is denoted by us, in strip windings, the voltage between turns of two adjacent layers is always us. In contrast, in traditional windings, this voltage reaches a maximum value of maximum value of (2n – 1) × us, as illustrated in the diagram below.

Transformers with strip windings have a higher resistance to impulse voltages and industrial frequencies, and a lower likelihood of localized partial discharges. Additionally, strip winding significantly reduces the axial forces caused by short-circuit currents.
In medium-voltage windings, the voltage is divided among the turns based on the winding design. For strip windings, the voltage between turns in adjacent layers is consistent. However, in traditional windings, the voltage between turns can reach a maximum value determined by the winding configuration. This distribution ensures that the voltage stress is managed effectively across the winding, contributing to the overall efficiency and reliability of the transformer.
5. Characteristics of MV/LV transformers
Table 1 – Standard Characteristics
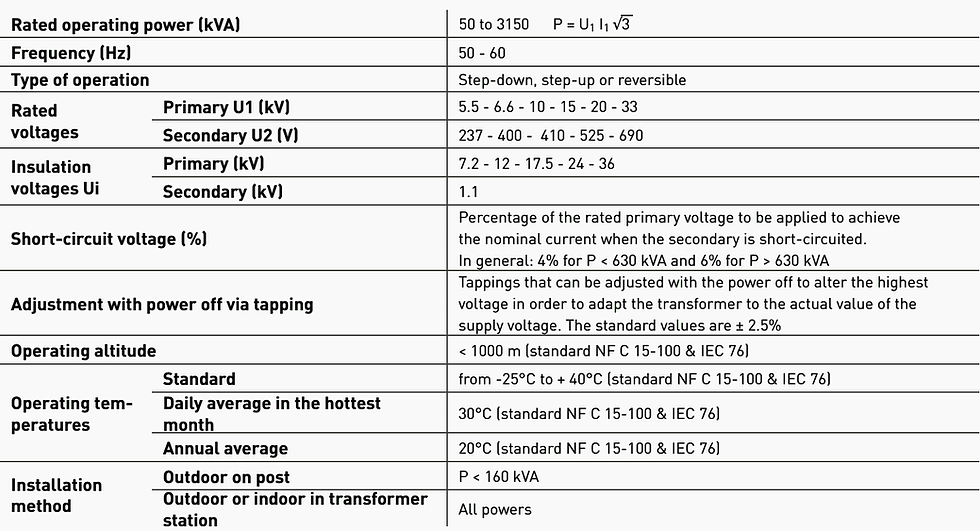
Table 2 – Characteristics connected with the construction method

6. Primary and Secondary Connection Configurations
Symbols are used to designate the connections in electrical windings. Internal windings can be connected in star (Y), delta (Δ), or zigzag (Z) configurations. Depending on the connection method, the system of induced voltages on the low-voltage side is out of phase with respect to the average voltage by angles that are multiples of 30°.
The winding connection method for three-phase transformers is identified by three letters: uppercase letters (A, B, C) for the primary windings and lowercase letters (a, b, c) for the secondary windings.
Y–star connection
D-delta connection
Z-zigzag connection
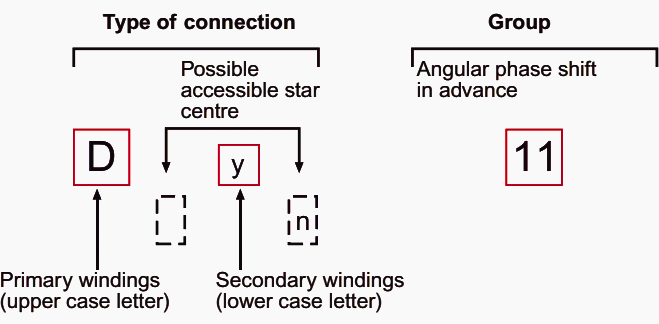
The phase shift can be divided into four groups, each representing a different phase displacement:
Group 0 – no phase shift
Group 11 – 330°
Group 6 – 180°
Group 5 – 150°
Selecting the appropriate transformer switch-ON unit is crucial for determining the operating regime based on the load. Ideally, the load should be balanced across all phases, but achieving this balance is often challenging.
Understanding the phase shift between primary and secondary phases is crucial. The table below illustrates the typical insertion diagrams for reference.
Table 3 – Typical MV/LV transformer connection configurations

6.1 Time Index
The designation of the connections (by letters) has an additional number that indicates the angular phase shift, for example Yy6, Yd11, Ynyn0 (external neutral).
In electrical engineering, the phase shift angle between primary and secondary voltage vectors of a transformer can be expressed using a time index instead of degrees. This method is often more descriptive and practical. For example, in a clock representation, each hour represents a 30° phase shift. So, a 1-hour shift corresponds to a 30° phase shift, a 2-hour shift to 60°, and so on. This approach helps in visualizing and understanding the phase displacement more intuitively.
The voltage vector on the primary side is assumed to be positioned at midday. The time index indicates the position of the corresponding vector on the secondary side.
Example: Time index 5 (phase shift 150°)

6.2 MV/LV Transformer Common Couplings

6.3 Coupling group
For two three-phase transformers to be able to operate in parallel, they must have:
A ratio of their power < 2
The same technical characteristics (transformation ratio)
The same short-circuit characteristics (% of voltage)
Compatible star or delta connections
Identical time indices (terminal to terminal links) or belonging to the same coupling group if the operating state is balanced.
Parallel operation of transformers from different vector groups is possible by modifying the connections. However, it is essential to submit these modifications for the manufacturer's approval to ensure safety and compatibility.


Reference: | Power balance and the choice of power supply solutions by Legrand |
Format: | |
Size: | 10.57 MB |
Pages: | 88 |
Download: |
Comments